In today's fast-paced industrial world, custom manufacturing is becoming increasingly relevant. This post will explore the fundamentals of custom manufacturing processes, shedding light on what they involve, their benefits, and why they are crucial for businesses aiming to stay competitive in a dynamic market.
Custom Manufacturing Defined
Custom manufacturing refers to the creation of products that are tailored to specific requirements or specifications of clients. Unlike mass production, which focuses on producing large quantities of standardized products, custom manufacturing is more adaptable. It allows for unique designs, materials, and functionalities that cater directly to consumer needs.

One of the primary advantages of custom manufacturing is the ability to produce high-quality items with enhanced capabilities that mass-produced goods often lack. For instance, an automotive company may require a specialized tool that fits its production line precisely, something that wouldn't be feasible through off-the-shelf solutions.
The Importance of Custom Manufacturing Processes
Understanding custom manufacturing is essential for various industries, including aerospace, automotive, medical devices, and consumer goods. These industries benefit from custom manufacturing in several ways:
Improved Product Quality: Since products are made to precise specifications, the overall quality is typically higher. This can lead to better performance and customer satisfaction.
Enhanced Flexibility: Custom manufacturing allows businesses to change their designs rapidly based on the market demand or technological advancements.
Cost-Effectiveness: While the initial setup for custom manufacturing can be more expensive than mass production, it can save money in the long run, especially when considering defects and rework costs.
Competitive Edge: By offering unique products, businesses can differentiate themselves in a crowded market. This uniqueness often leads to increased customer loyalty.
What is Customization in Manufacturing?
Customization in manufacturing revolves around modifying existing designs or producing new items that comply with specific client demands. This can include altering dimensions, integrating different materials, or completely redesigning a product based on feedback or technological needs.
For example, a company might require a specific type of machinery tailored to its workflow. Instead of purchasing a generic model, opting for custom manufacturing allows them to obtain machines that fit precisely with their operations. Such personalization minimizes waste and maximizes efficiency.
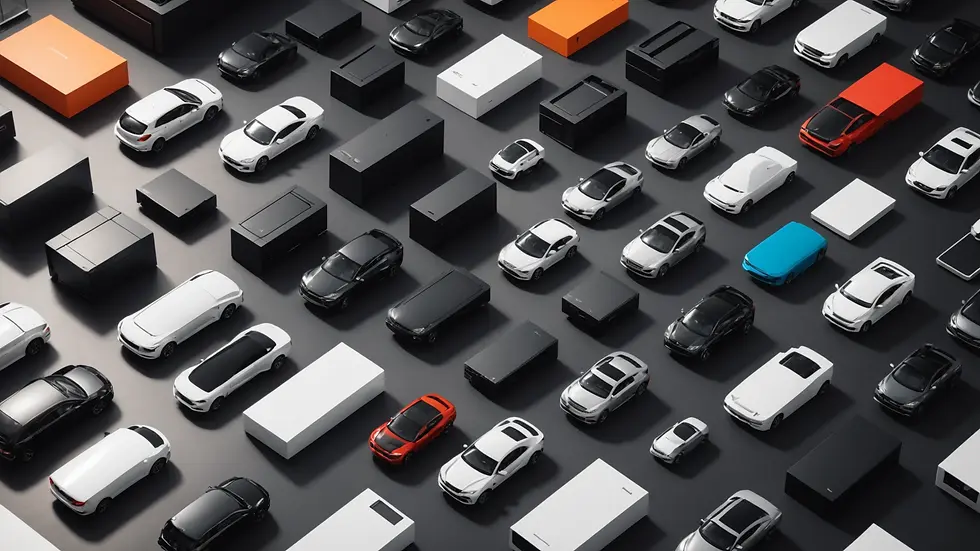
Customization can extend beyond just physical products. Services provided during the manufacturing process can also be tailored. Consider a company that not only manufactures a product but also requires a unique packaging solution that enhances the presentation and safety of the item during delivery.
Key Processes in Custom Manufacturing
1. Design Engineering
Design engineering is the first step in the custom manufacturing process. Engineers collaborate with clients to conceptualize and create detailed models tailored to specifications. Utilizing CAD (Computer-Aided Design), companies can visualize their projects before actual production begins.
2. Prototype Development
Once a design is approved, the next step is prototype development. This phase allows companies to create a working model of their product. It serves as a proof of concept, enabling clients to test the design and functionality before full-scale manufacturing begins. Feedback gathered during this phase is critical as it helps refine the design further.
3. Production and Assembly
After successful prototyping, production and assembly commence. This phase may involve various techniques and equipment, including CNC machining, 3D printing, and traditional methods. The choice of technique often depends on the product's intricacy and material requirements.
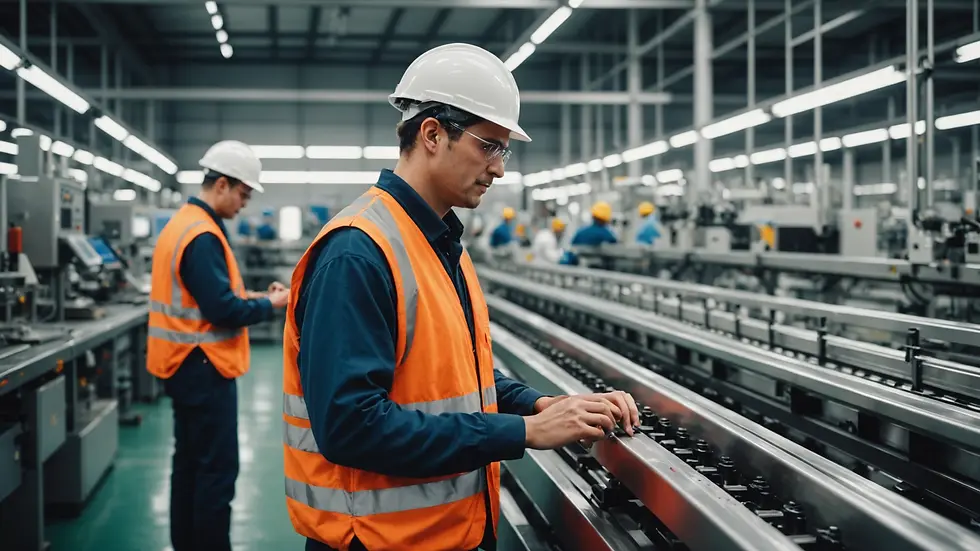
4. Quality Control
Quality control is an integral part of custom manufacturing. Each item produced must meet stringent standards. Companies usually implement rigorous testing protocols to ensure that the final products perform as intended and comply with any regulatory requirements.
5. Final Delivery
Finally, once all quality checks are completed, the products are packaged and delivered to clients. Effective communication throughout the latter phases ensures that customers are satisfied with their orders and that they fulfill their expectations regarding timelines and quality.
Final Thoughts on Custom Manufacturing
The rise of custom manufacturing processes is a testament to the ever-evolving landscape of industry demands. Companies looking to thrive in today’s market must consider incorporating custom solutions to enhance innovation, product quality, and customer satisfaction.
By understanding these fundamental concepts of custom manufacturing, businesses can leverage custom manufacturing services to stay ahead of the competition and successfully cater to their clients’ needs.
Embracing custom manufacturing is not merely an operational choice but a strategic imperative that aligns with a business's long-term goals. So, whether you're a small startup or an established enterprise, investing in custom manufacturing knowledge and capabilities can pave the way toward achieving sustainable growth in your specific industry.
Comments